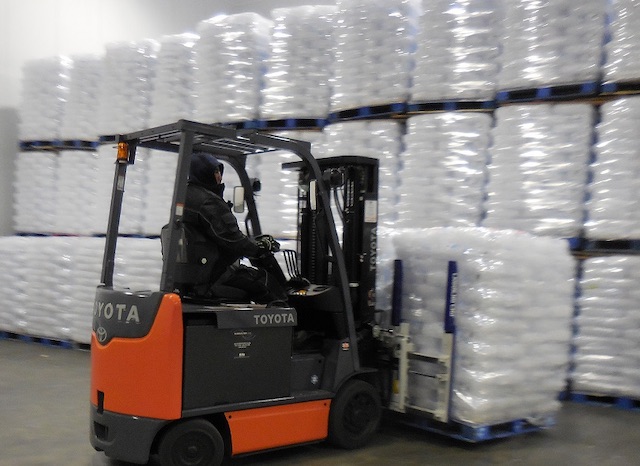
One of the most important tasks that face cold room forklift users is the need to reduce condensation on a forklift while in warm temperatures, helping to prevent freezing when re-entering frigid spaces. Freezing can cause inefficient operation and downtime for the forklifts, resulting in lost throughput for the cold operations. A few best practices can help to prevent these inefficiencies, providing maximum use of the forklift fleet while maintaining your return on investment for your capital equipment.

Storing your Cold Room Forklift
The storage of your forklift is key to maintaining efficiencies. Sustained storage in freezing temperature can lead to breaking parts and battery inefficiencies. The best practice for storing a cold room forklift when not in operation is to do so outside of the cold area. But this presents its own condensation challenges. One solution is to store your forklifts in a dry area that is just above freezing temperature in order to ensure that condensation forms slowly or not at all.
However, this isn’t always possible. When that’s the case, you need provide enough time for the forklift to rest outside of the cold facility and in warm temperatures for the condensation to form and evaporate. Operating too early before evaporation can lead to freezing. The process can be accelerated by the use of fans in the storage space.
Why Are Lithium Ion Batteries Best for Forklifts?
These batteries offer a broad range of advantages for many warehouses and distribution centers because of the ease of charging. Opportunity charging provides the ability to plug in the battery without taking it out of the forklift, as opposed to swapping batteries its lead-acid counterpart requires.
High-throughput operations tend to see the biggest bang for their buck when using LIBs, but the benefits are broader than just the return on investment. As the technology behind these batteries advances, we see a broader range of companies using them.
- Improved Energy Bills - Lithium-ion forklift batteries are more energy-efficient and charge faster than lead-acid batteries, saving you time and money.
- Equipment Longevity - Your lithium-ion battery will typically last two to four times longer than a lead acid battery. This helps you keep up with those long workdays.
- Less Downtime - Lithium-ion batteries don’t need to be swapped out and can be opportunity-charged during operator breaks.
- Reduced Labor Costs- Lithium-ion forklift batteries don’t require traditional maintenance like watering or equalizing.
- Better Productivity - Operators can enjoy longer run-times and zero decline in performance as the battery discharges with forklifts powered by lithium-ion batteries.
- Less Environmental Impact - Lithium-ion batteries have no emissions and their longevity may mean less battery disposal in the future.
- Onsite Real Estate: Businesses can reclaim the area being using as a charging room for additional storage.
Using a Cold Room Forklift in Changing Temperature Applications
In many applications, the cold storage environments are intermixed with warmer spaces. For example, movement from a cold room to a cold truck may require the passing through a warm docking area. 3PL applications may be storing a variety of goods, some cold and some ambient. These challenges present a situation where some condensation is inevitable. But there are certain steps that can help.
If it is within your operational budget to maintain multiple forklifts with specialized areas of operation, that can help prevent potential wear from changing temperatures. It will increase necessary touches to pass product between pieces of equipment at the door of a cold storage area, but depending on your particular circumstances, this could provide value in increasing the operational efficiency of the forklifts. You’ll need to perform a site analysis to decide if this is a useful approach.
If maintaining multiple forklifts is out the questions, you can still take steps to help prevent problems from condensation. For example, facility design becomes key. Optimizing the routes that cold room forklifts must take between the cold environment and the truck to be loaded can help ensure that they stay in cold spaces as much as possible. Additionally, order of operations becomes key. Limiting the amount of times a cold room forklift needs to change environments can reduce the chances for condensation to form.
Choosing the Right Cold Room Forklift
Electric forklifts are those used in cold applications and selecting the right one can have a major impact on efficiencies and ROI. Forklifts with fewer moving parts and wires reduce component parts’ heat production and the chance of condensation entering into the nooks and crannies of the forklift. For example, modern electric forklifts are engineered with as few moving parts and AC motors and controllers to reduce internal component heat generation. These small engineering feats can have a lasting impact on operational efficiency.
While condensation isn’t the only challenge facing cold room forklift operators (we haven’t even touched on safety issues in a potential slippage environment), it is one of the most pressing when it comes to the mechanical operation of forklifts in cold environments. For more ideas about cold storage, check out our whitepaper on cold storage in the food supply chain.
Thank you for sharing this informative blog. It's extremely good and very helpful for me.
ReplyDeleteWarehouse Control System